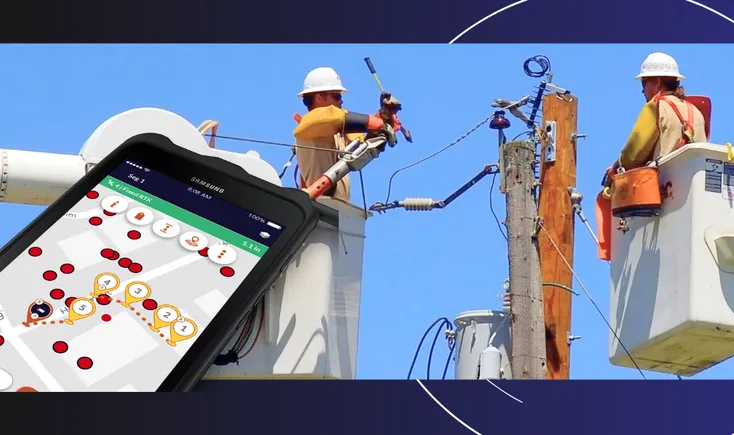
Congratulations!
Your utility has successfully implemented a cutting-edge ADMS application. Your GIS team has spent months working closely with the implementation team to clean and correct the data within the GIS application. The teams have validated voltage and phasing, eliminated loops, resolved open points, populated missing attribution with default values, and ensured the connectivity of circuits and devices for every feeder in your distribution system.
This extensive data validation, updating and cleanup effort was costly, but it should significantly enhance the management of your transmission and distribution (T&D) operations. It will improve your reliability statistics, boost customer satisfaction ratings and earn you recognition with the Public Utility Commissions in your service territory.
Now comes the hard part: Keeping your GIS and ADMS current
Utilities must recognize that their efforts to clean up and validate their GIS Connectivity model is not a one-time task performed during ADMS implementation As new or replaced assets are installed in the T&D system, those new assets must be updated into the GIS in near real time.
The data and attribution requirements of ADMS are far more demanding than the current data and general mapping requirements or your legacy GIS. Real-time access to new construction data is critical for the effective use of ADMS applications. For example, if new switching devices are not updated, you won’t be able to optimize your outage isolation switching orders. Without the new transformer data in GIS, ADMS won’t be able to account for transformer load-splitting results, impacting your Reliability Statistics. Additionally, you won’t be able to optimize FLISR if the assets are not accurately accounted for in GIS. One Tier 1 utility reported that 2 years after cleaning their GIS data before launching ADMS, 50% of their substations are no longer analysis-ready in ADMS due to the lack of a process to continuously push high-fidelity construction data to their GIS in near real time.
The most effective time to collect new asset data is at the time of installation. For ADMS, simply knowing that the installed transformer is a generic 50 kVA unit is not enough. ADMS requires detailed data about that specific transformer, with unique attributes that vary across each device.
If you don’t reimagine your current data capture processes, you’ll quickly lose the value of your ADMS investment.
Field workers and installers are the best sources for identifying newly installed asset data—they know what was installed, where it was installed, and when it was installed. But collecting data in the field using traditional manual, paper processes is not viable in light of ADMS data requirements. The answer is to utilize modern and automated data collection technology to simplify the data capture process. Barcodes, QR codes and RFIDs are the obvious solutions. These scanning technologies are widely used in everyday life—whether at the grocery store, coffee shop, or hardware store—and can be easily leveraged for asset tracking.
Strategies for optimizing ADMS
Ensuring that high-fidelity, accurate data is fed to ADMS not once, but on a perpetual basis, requires a different approach. By providing a “digital thread” from planning through construction execution, through close out, Digital Construction Management (DCM) solutions can provide a seamless process integrated with GIS that provides continuous updates to ADMS.
DCM solutions start with a fully digital job packet that includes design and Compatible Unit (CU) data. Field crews use a mobile application and barcode scanners to easily and accurately collect as-built data on the job site. But the true value for utilities is the post-construction processing of the field collected data into the various Systems of Record enabled with a DCM application.
Through the use of near real-time communications via “the cloud”, back office staff can review and approve as-built changes to the design. As-built changes can easily be captured in a single workflow whether spatial or attribute data, with the system able to report back the compatible units for WMS / accounting and spatial data / attributes for GIS. Any approved changes can be processed into the GIS and WMS applications through partial posting or at the approval of the entire work order. GIS data can then be reflected in ADMS to ensure the system is operating with a “digital twin” of actual field conditions.
This rapid post-construction processing of completed Work Orders ensures that all Work Order close-out processes are completed quickly, reducing their impact on CWIP and AFUDC levels and enabling the rapid inclusion of new assets into the Utilities Rate Base for cost recovery.