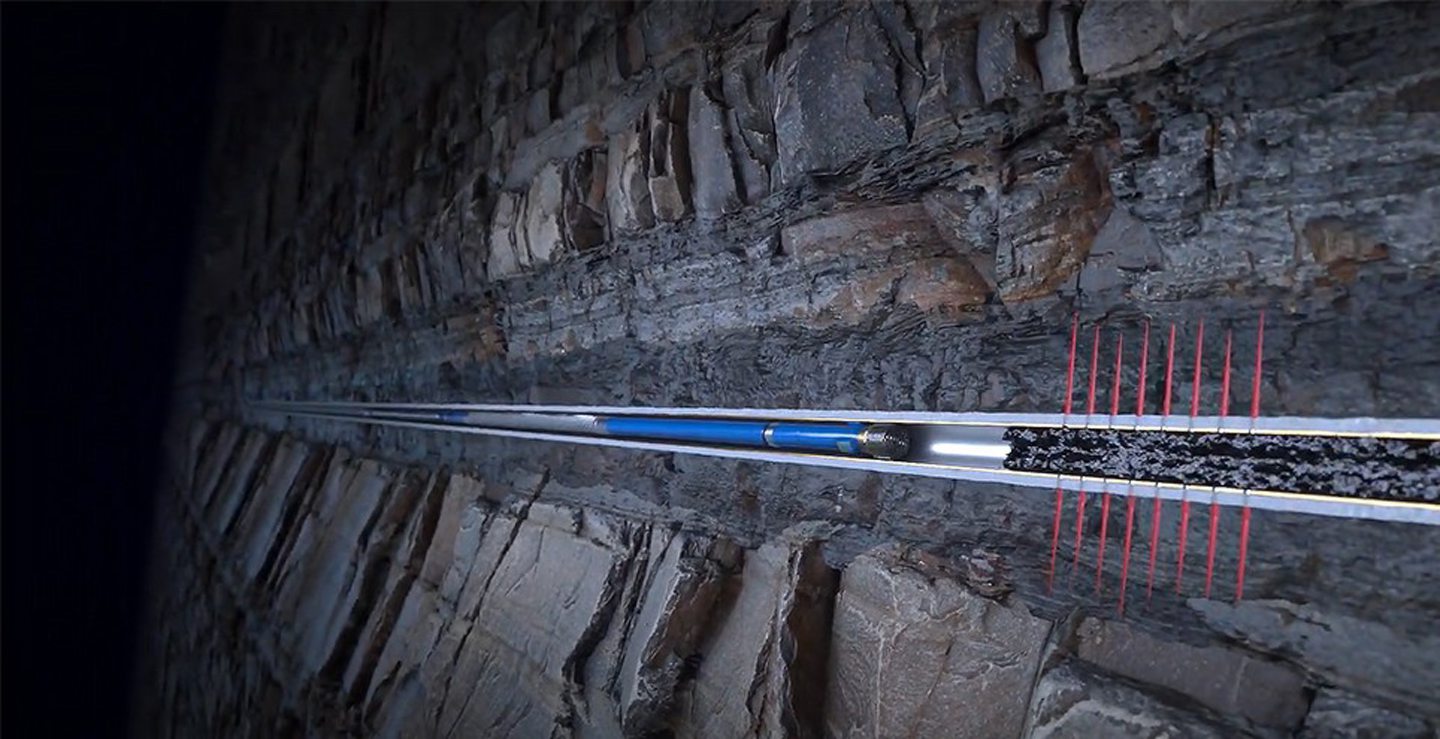
Leading services company Reservoir Group has found an innovative solution during coil tubing operations that promises to save operators time and money.
For decades, gathering critical data during coil tubing deployment involved separate logging runs, adding time and cost to well monitoring.
That’s because traditional methods required wireline or slickline deployment of gauges, forcing operators to interrupt operations to retrieve vital information.
Recognising the inefficiencies of this approach, Reservoir Group developed a system of gauges mounted directly on coil tubing.
This breakthrough technology allows operators to collect pressure and temperature data, assess wellbore integrity, and detect leaks during the drilling process itself.
An early deployment of the system saved one company $65,000.
How groundbreaking technology works
Reservoir Group’s flow-through gauge carrier is a non-magnetic, 718 nickel alloy tool that seamlessly integrates with coil tubing operations. The carrier can be equipped with a range of memory tools, including:
- Dual pressure and temperature gauges
- Acoustic logging tools
- Gamma ray/CCL (casing collar locator)
- Electromagnetic logging tools
By deploying these gauges on coil tubing, operators can simultaneously conduct standard well interventions, such as jetting cleanouts, while collecting essential well data. This eliminates the downtime typically associated with logging runs and ensures that valuable insights are gathered without disrupting the workflow.
Key benefits of Reservoir Group’s solution
Compared to traditional logging methods, Reservoir Group’s coil tubing solution offers several distinct advantages:
- Efficiency Gains: Since the gauges are deployed on coil tubing during existing operations, there’s no need for an additional logging run, significantly reducing rig time.
- Cost Savings: Eliminating separate wireline or slickline runs results in substantial cost reductions. A recent case study demonstrated savings of $65,000 for a single well intervention.
- Versatility: The technology supports a wide range of well environments, from pressures of 150 psi to 30,000 psi and temperatures between -20°C and 200°C.
- Minimal Operational Disruption: The gauge carrier allows for fluid circulation and tool operation below it, ensuring that conventional coil tubing interventions can proceed uninterrupted.
- Enhanced Data Collection: With the ability to deploy multiple types of sensors, operators can obtain a comprehensive view of downhole conditions in a single run.
Real-world success
So, the theory is sound, but how has it worked in reality?
A major operator recently incorporated Reservoir Group’s gauge carrier into a coiled tubing intervention campaign alongside a jetting cleanout.
The well, with a depth of 5,203m MD (17,066ft MD) and a bottomhole temperature of 189°C (372°F), required high-temperature QM200 quartz gauges mounted on the nickel alloy carrier.
The results were impressive.
The gauges successfully retrieved pressure and temperature data, while realising significant cost savings of $65,000 by eliminating a separate logging run.
The system seamlessly integrated with coiled tubing operations, proving the carrier’s effectiveness in high-temperature and corrosive environments.
The innovation behind the development
Reservoir Group’s gauge carrier was born out of internal innovation. The company operates in both well monitoring and well intervention, supporting the coil tubing market. By leveraging its expertise in both areas, Reservoir Group identified an opportunity to merge these capabilities, leading to the development of a more efficient solution.
The entire process — from initial concept to deployment — was completed within approximately eight months. The technology was ready for field trials within three months, thanks to the company’s existing intellectual property and expertise in coil tubing and logging tools.
The general manager for Europe and Africa at Reservoir Group said: “We pride ourselves on providing new innovative ideas which improve efficiency and save our clients money. To our knowledge, we are the first company who is providing this solution in the industry.”
Now Reservoir Group is ramping up marketing efforts to expand adoption. Given the substantial cost and time savings, the company anticipates widespread interest from operators looking to optimise their well monitoring practices.
To learn more visit Reservoir Group’s website.