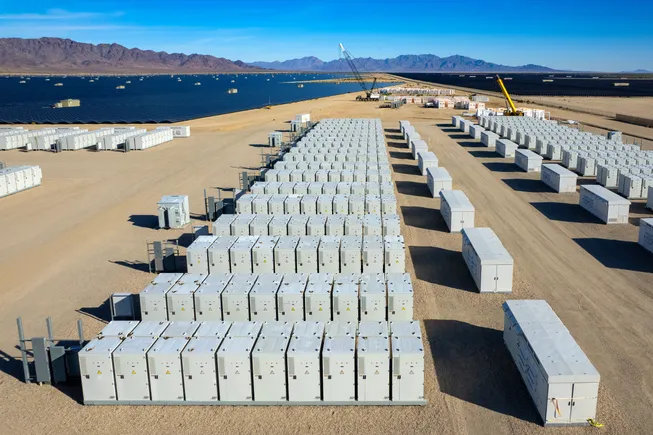
Karl Littau is the chief technology officer of Sakuu, a San Jose-based company providing commercial-scale printing equipment and technologies to the battery industry.
The recent battery fires at the Vistra Moss Landing Energy Storage Facility on the California coast are a tragedy.
A large regional energy source was ruined, nearby residents evacuated and already there are lawsuits and questions about toxins released into the environment.
Battery energy storage system, or BESS, facilities are essential for leveraging renewable energy resources like solar, since they capture daytime electricity production and supply it to the grid after sundown when demand remains high. But communities may become more hesitant about hosting these facilities.
So it’s a tragedy because society desperately needs more renewable energy, more grid storage and more BESS facilities — and this could slow things down. (Lest we forget: Non-renewable energy production is not free from fire risk, as residents of Martinez, California, can attest.)
The saddest thing is that BESS fires like Vistra’s are entirely preventable. It all comes down to how batteries are made.
Understanding batteries
I don’t want to minimize this catastrophic fire, but let’s be clear: Lithium-ion batteries are incredibly safe. There are literally billions of them in use every day around the world, functioning reliably and without incident. But changing the way they are manufactured will make them even safer and virtually eliminate the possibility of fires.
Lithium batteries need no air to burn. Above a certain temperature, a battery fire is self-sustaining — it can’t be “choked off” with traditional firefighting techniques. It would probably burn on the moon! All firefighters can safely do is wait for it to burn out and keep it from spreading.
As with nearly all lithium-ion batteries, BESS batteries are made of thin layers of anode and cathode materials interdigitated together and encased in aluminum and copper. A small manufacturing flaw in one cell may cause an internal short that produces heat. And due to the design of the layers and the mixed metal conductors, all the cell’s energy discharges within seconds. Those failures are catastrophic. It gets so hot, so fast, that it ignites nearby batteries, and eventually everything around them, burning so intensely that fire suppression systems can’t stop it. There are some approaches to mitigate this risk, like using lower energy LFP batteries. But even with those, a short still causes failure and can generate enough heat for fire.
There is a way to avoid these fire risks altogether.
Lithium-ion battery cells made with composite conductive materials — or polymeric current collectors, PCC — are built with a different architecture. When there is a short, they continue to function. Energy eventually dissipates, but it happens gradually over the course of hours. There is no catastrophic heat production, ignition, or “thermal event” (fire).
If a PCC battery fails, it’s a warranty issue. No one needs to call the fire department.
Making safer batteries
A PCC cell is a series-connected battery, not a parallel-connected or interdigitated battery like those now used in BESS facilities. It’s still made layer by layer, but the layers are connected directly, one on top of the other, and current moves from one layer to the next over the entire surface of each layer. There’s no need for aluminum or copper. Instead, a thin conductive polymer film loaded with a little bit of carbon is used, and current flows vertically up a chain of sealed layers. It cannot produce fire.
This is not a “new” lithium-ion battery architecture. Plenty of people are familiar with it and companies as formidable as Apple have explored it for safer batteries. But one of the reasons they and others could never move forward with PCC batteries is that there was no way to mass produce them.
In standard battery manufacturing, all the cell layers are interleaved together, the electrolyte floods over them, and everything is packaged with a single seal. Worldwide, this “wet process” is how lithium-ion batteries have been made for over 30 years!
To build a PCC battery, every single layer within it functions as its own individually sealed battery — you can’t flood the whole thing with an electrolyte because that would short out the battery. It won’t catch fire, but it also won’t work. You could construct the individual cells “by hand” separate from the standard fabrication process, but then you would be manufacturing a battery exponentially more expensive than everything else on the market — and no one is going to pay that much for a battery no matter how safe it is.
But upgrading the standard equipment in existing battery manufacturing plants lets you use a multimaterial “dry process” to produce batteries with a sealing material right around every layer individually. Dry electrode technology makes PCC batteries imminently feasible. And to make a long story short: Yes, we now have that technology; Yes, we have systems capable of mass production; No, it won’t increase the cost of making the battery — if anything, it should make it cheaper.
And, of course, they don’t catch fire.
The Vistra fire represents a safety issue that only exists because 20th century manufacturing equipment doesn’t produce 21st century batteries.
Simply put, better manufacturing processes produce better batteries. That’s the truth for desperately needed grid storage, BESS facilities and countless other battery-powered innovations.